After offering a few years of harpsichord regulation, voicing, & repair workshops it it became clear that some tools and supplies used in the program are not readily commercially available. This seemed like a disservice, a missing piece in our goal to equip technicians and musicians to properly care for their instruments. I offer a kit of some of the tools and some supplies used in harpsichord & clavichord service that are not otherwise readily available.
Contact
➤ LOCATION
Serving the greater Boston area
☎ CONTACT
Louis del Bene, RPT
louis@brevetpiano.com
(336) 271-5923
Tools
The harpsichord voicing/regulation tool kit includes the following:
(1) Voicing Block, (1) Capstan Turner, (4) Ghosting Shims - 2x .020” & 2x .015”, (1) Timing Wedge, (1) Damper Trimming Block, & (1) String Length Template. It also includes a supply of Delrin strips at .020” thickness (x10), and Delrin strips at .015” (x10).
The cost for the kit is $225 (USD), plus shipping.
Ghosting Shims (.015” Red and .020” Blue)
Ghosting Shims are made of Delrin, & labeled with ink - blue indicates .020” thickness and red indicates .015” thickness.
Ghosting is the process of cutting plectrum to length. This is done before Voicing.
The 8’ registers on many instruments work well with a total of .040” of overall travel from “ON” position to “OFF” position. In ON position, the plectra should engage with the string by about .020”, in OFF position, the plectra should miss the string by about .020”. This means that when the register is right in the middle (in GHOST position), the string should be made to sound, but not plucked. We listen for the tip of the plectrum to graze its string in ghost position.
To achieve GHOST position, sample plectra are cut to length across the scale of the instrument (all the C’s for example). Then the register is set up as described below - with a Ghosting Shim on either side of the adjustment screws at the ends of the slide, each plectrum should graze its strings. It should be confirmed that in the OFF position there is at least 1.5mm of space between the back of the jacks and the neighboring string. If not, adjustments must be made: plectra must be shortened. Once GHOST position is decided, all plectra can be cut to length so that they graze their strings.
A good starting point for plectra length for the back 8’ is 5.0mm in length from the face of the tongue. A good starting point for the front 8’ is 4.5mm in length from the face of the tongue. For the 4’, the goal is to make the plectra as long as possible without getting too close to the neighboring string in the OFF Position (often 4.0mm is a good target).
Voicing Block
The block is held inside the hand, with the loop around the ring finger. The Jack is upside down, with the plectrum supported by the top surface of the voicing block.
Voicing Block: For Ghosting
Made of hardwood with a light coat of shellac, brass wire, and ink, one function of the Voicing Block is to set the length of each plectrum in the process known as ‘Ghosting’.
‘Ghost Position’ is somewhere in between full ‘On Position’ where all plectra are fully engaged with their strings, and full ‘Off Position’ where all plectra are fully missing their strings. See the Ghosting Shims description above for more information on how to set Ghost position.
This process begins with the register in Ghost Position, and with all plectra installed and too long. Each plectrum is cut so that it neither misses nor plucks the string. Another way to say this is that the plectrum should ‘graze’ the string. A pitch should be heard when the key is played, but there should be no ‘pluck’, and no additional resistance felt at the key as the plectrum passes the string.
Cuts are made with the jack upside-down, and the plectrum fully supported by the single bevel (all black) surface of the Voicing Block. A standard razor blade (such as Excel #9 hard backed blade). With the spine of the razor blade fully in contact with the body of the jack, and the plectrum supported by the voicing block, small amounts of material can be removed to achieve the desired length.
The angle of cut is very important to the note’s ability to reset and therefore repeat in playing. This is a by-product of the angle created by the razor blade when cut to the proper length with the spine of the razor blade fully in contact with the body of the jack.
The block is turned upside down from the orientation used when Ghosting. The loop is still around the ring finger, and the thumb is held well below the top surface to avoid being cut by the followthrough of the carving stroke.
Voicing Block: For Voicing
With all plectrum ghosted (cut to the proper length), the Voicing Block can be turned over & voicing can begin.
When doing service work, replacing one or two plectra may be all that is needed - in those cases, the underside of the plectra is carved to match the tone & volume of its neighbors. When replacing all plectra on an instrument, a dynamometer (250g maximum) is often helpful to set the pluck force on a few notes across the scale of the instruments (all C’s for example) based on a known range of acceptable forces for a given instrument. Once they are cut in, the rest of the instrument can be cut in to match, dampers can be installed, and the voice can be refined.
Simplified: Voicing = Removing the Noise while Leaving the Tone.
In short, the volume should be even from note to note, and balanced between registers.
Damper Trimming Block
Made of a variety of species of wood with a light coat of shellac, the Damper Trimming Block is used to trim damper cloth that is too long. When the cloth is too long it can create “Damper Interference” with the strings of neighboring notes. The damper trimming block allows for clean and accurate trimming.
Timing Wedge
Made of American Linden (or other hardwood) with a light coat of shellac, and marked with ink and graphite, the Timing Wedge is a measuring tool used to evaluate, set, and check the ‘stagger’ of pluck for the various registers on a given note.
The wedge is placed below the key, and with a light touch the key is depressed while the wedge is pulled out from under the key. Each line represents 10mm. The stagger should produce a particular ‘song’ for each instrument, separating the plucks enough for the musician to control their playing, but not so far apart that excessive key dip is necessary to complete the cycle and provide some ‘aftertouch’.
The 4’ should generally pluck first, then the back 8’, finally the front 8’. The space between plucks of the 4’ & back 8’ registers will be less than the distance between plucks of the back 8’ and front 8’ registers. There should be more space between plucks in the bass than in the treble, with an even & gradual change between the two extremes.
The point of regulation is to make the function of the action regular & reliable.
Capstan-Style Bottom Screw Turner
Bottom Screw Turner
Made of stainless-steel wire, the Bottom Screw Turner is used to set jack length and therefore pluck timing when capstan style bottom screws are present.
This tool is used to set the first-plucking register (usually the 4’ register). A notes is first set to ‘dead under’, then the jack is shortened to create the appropriate amount of lost motion before string contact is achieved. This allows the space necessary for the plectrum carrier (tongue) to move past the string and re-set. Once jack length is set for the first-plucking register the Bottom Screw Turner is used in conjunction with the Timing Wedge to adjust the length of the jacks in order to set desired pluck timing between the remaining registers.
For most bottom screws, a tolerance of ’15 minute’ turns (1/4 turns) are the smallest increment of adjustment a technician should use.
String Length Template
String Length Template
Made of ink on mylar, the String Length Template is used as a guide to cut wire to length when stringing, re-stringing, or replacing individual wires. It can be used as a starting point for most harpsichords and clavichords.
This tool gives a reasonable starting point for setting the length of the wire needed to achieve desirable coils around a tuning pin. The tool is taped to the stretcher/cornice with the end lined up to (or near) the tuning pin hole being used. The wire is then pulled, along with template directly behind/below the wire. The wire is then cut to the length indicated by the template based on the diameter of the wire being installed. The wire can then be wrapped around the tuning pin, and the pin installed into the appropriate tuning pin hole.
The goal for individual wire replacement is that the coil and down draft generally match the original/surrounding strings.
The goal for restringing is that there is enough tight wraps of wire around the tuning pin to achieve stable tuning (usually about 5mm), and enough space below the tight wraps to achieve desired down draft (usually between 2.5°-5°).
Supplies
Plectra Strips - Blue = .020” / Red = .015”
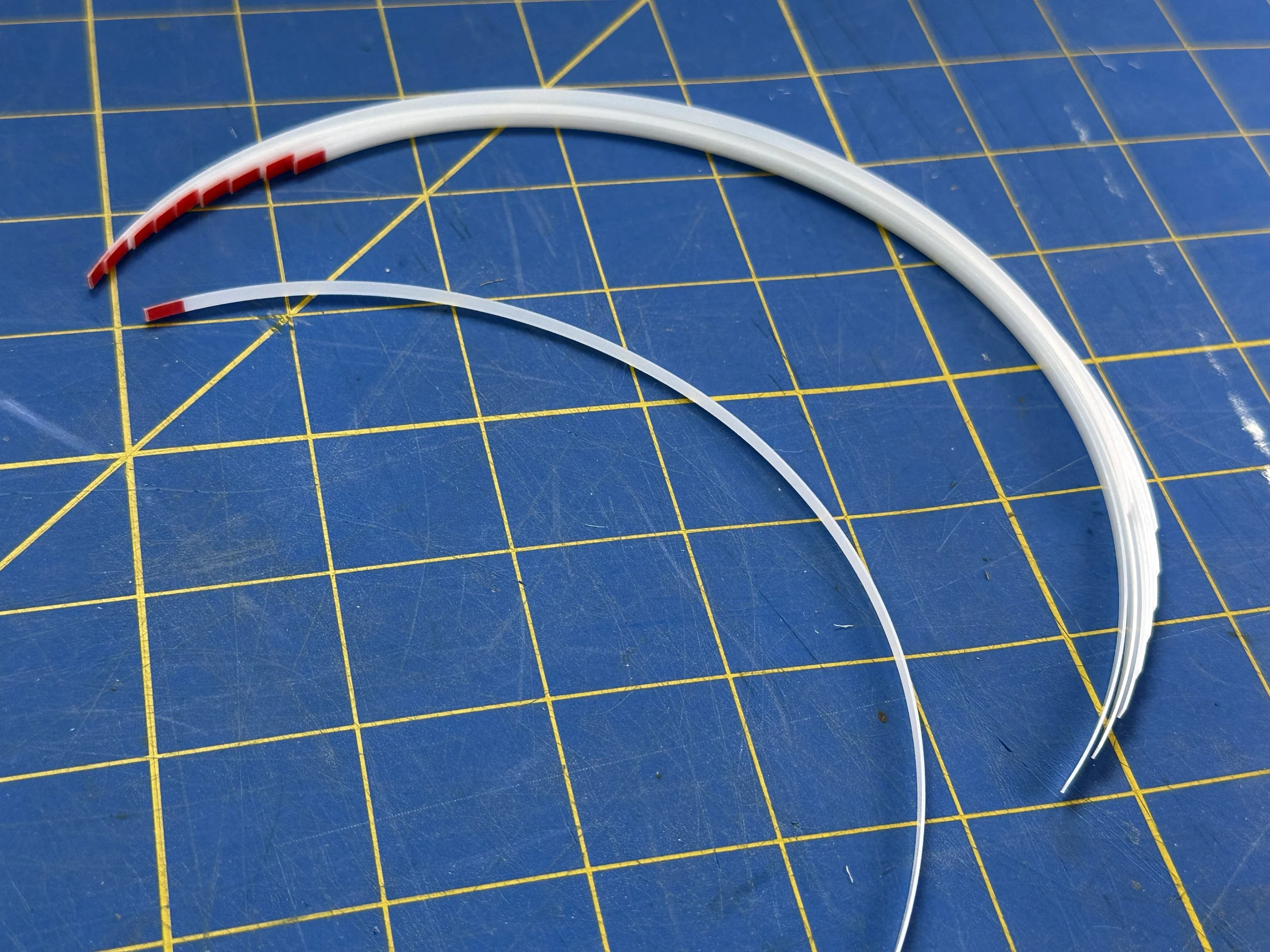
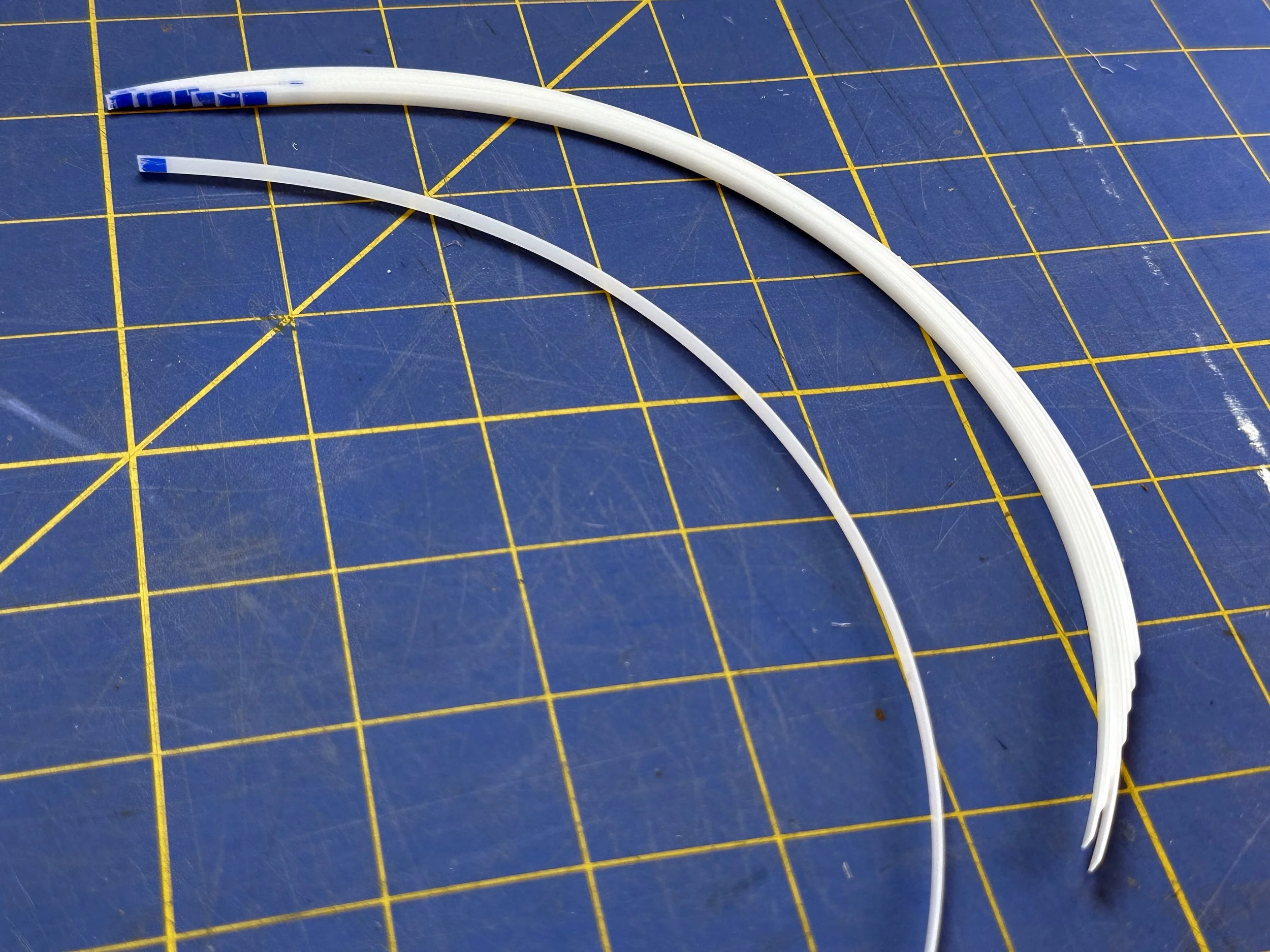
Plectra Strips are made of Delrin labeled with ink. The strips measure 2.7mm wide (+/- .3mm) and 9” long. They can be used to replace plectrum of many instruments made from the 1960’s to present, which were fit with ‘plastic’ plectra.
They come in two thicknesses: .020” strips are labeled with blue and are used for 8’ registers. .015” strips are labeled with red and are used for 4’ registers.
They are sold in packs of 10 strips either blue (.020”) or red (.015”). The strips are packaged in clear plastic tubing with end-caps which works well for transportation and protection in tool bags.
$20 per pack of 10 strips.
String Packs
String Packs are made of a variety of materials - Red Brass (90/10), Yellow Brass (70/30), and a variety of iron and steel options are available. They are cleaned, given a hitch-pin loop, and cut too-long, ready for replacement.
When servicing one or more known instruments it is often a good idea to have a pack of pre-looped wire that is appropriate for when replacements are necessary. There are also times when an instrument is strung and wire is breaking regularly - in these cases, modifying the material used in a given section of an instrument may be a good idea. They can also be made to have on hand for the inevitable string replacement on any instrument that may be encountered.
String packs are made to order - prices vary depending on material used & size of order. Packs generally have 2 of each size brass wire, and 3 of each size iron/steel wire but special orders can be accommodated.